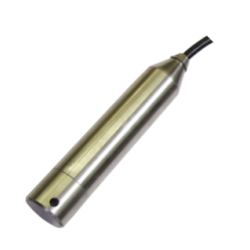
- hydrostatic level measurement
- stainless steel hanging dip probe
- ranges from 0,25 to 600 m W.S.
- easy installation and disassembly
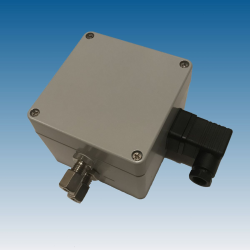
- measuring ranges from 0 - 100 mbar to 0 - 6 bar
- static pressure limit to 200 bar
- longtime stability
- shock resistance
- suitable for oxygen applications
- possibility to select the output signal
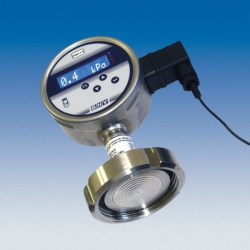
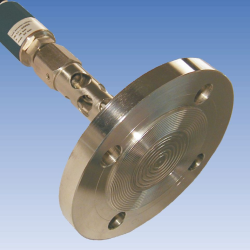
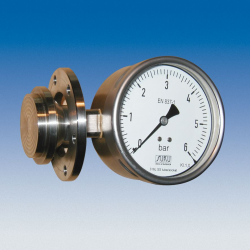
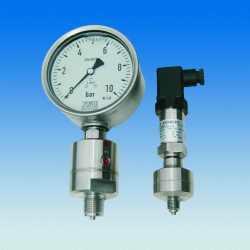
- It is used to effectively crush pressure because it allows the use of a very narrow throat cross section without the risk of clogging
- It is a simpler version of the K type separator.
- Connecting : G1/2”, M20x1,5, G1/4”, M12x1,5 according DIN 16288
- Body diameter: 40, 50, 60 mm
- The size of the diaphragm corresponds to the diameter of the body.
- Material: stainless steel (Monel, nickel, etc.)
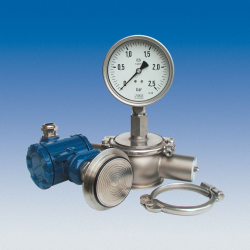
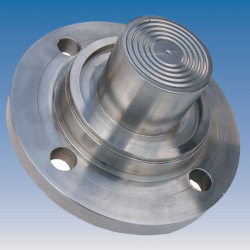
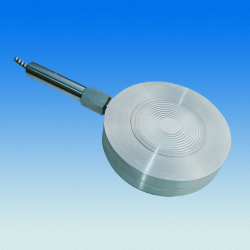
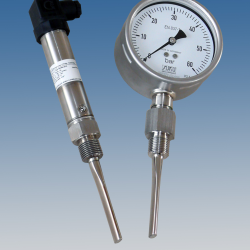
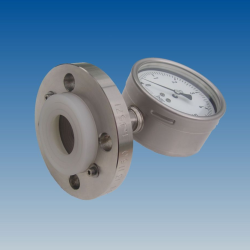
- The advantage of a semi-sealed diaphragm flange separator is a relatively larger diaphragm with respect to the smaller attachment dimension
- Flange dimensions according to EN 1092-1: DN 15, 20, 25, 40 (mm)
- Flange dimensions according to ANSI B 16,5: DN ½“, ¾“, 1“
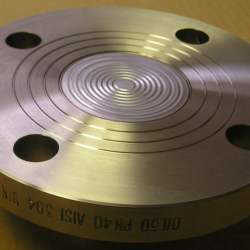
- The advantage of flanged separators (also called "open flanges") is the large dimension of the diaphragm, which is a prerequisite, for example, for accurately measuring lower pressures or for accurately measuring the pressure in the higher temperature range.
- Flange dimensions are according to ČSN 131160 resp. DIN 2501: DN25, 32, 40, 50, 65, 80, 100 (mm), possibly in inches according to ANSI 16,5.
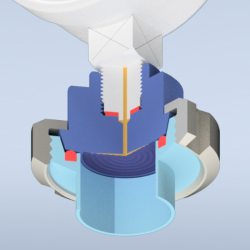
- connection with quick coupling with union nut according to DIN 11851
- conical neck (special design: threaded neck)
- dimensions DN: 25, 32, 40, 50
- used in the food industry
- also according to SMS, IDF and other standards
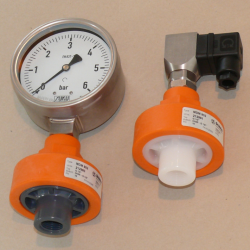
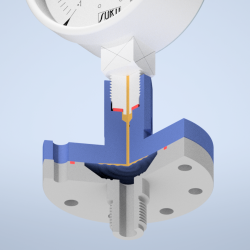
- Allows the use of large membrane properties at low attachment dimensions
- Connection: internal thread G1/2”, M20x1,5, NPT 1/2” (other subject to agreement)
- The separator can be dismantled and the interior space can be cleaned
- Tantalum membranes or PTFE protective films can be used to measure the pressure of aggressive chemicals; The bottom part can be made of durable plastic or a suitable lining.
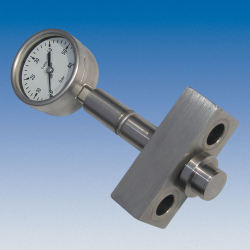
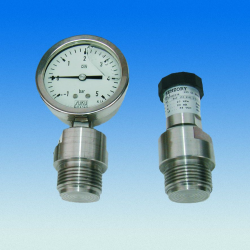
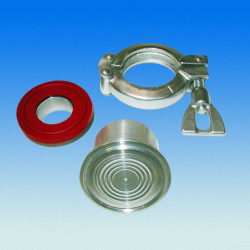
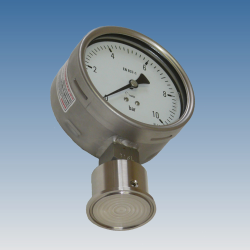
- Stainless steel
- Ranges from 60 kPa to 250 MPa
- illed with glycerine (optional)
- Bottom or rear connection
- Stainless steel manometers gauge DN63 or DN100
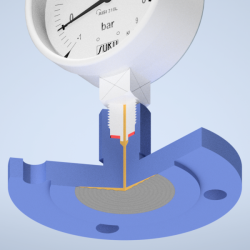
It is used to measure the pressure of liquids and gases if it is not possible for the measured medium to penetrate into the gauge or transmitter measuring device.
This need arises where they occur:
- Highly viscous liquids
- Solid particulate fluids, sedimentary sludge
- Hot liquids that solidify or crystallize when the temperature drops
- Aggressive fluids
- Requirements for perfect system cleanup
The solution consists in using a separating membrane and an inert liquid, that transfers pressure to the gauge or transducer measuring device.
We produce and repair many types of separators, different types of flanges and dimensions.
Gallery of chemical seals applications ...
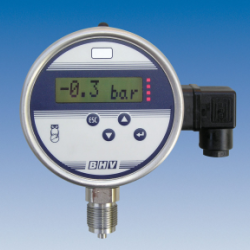
- LED with 4 digits or LCD with 6 digits
- pressure ranges from 0..60 mbar up to 0..700 bar
- accuracy 0.5% FS (combined error), option 0,1% of reading ± 0,05% FS
- explosion-proof design (ATEX)
- powered from a built-in accumulator
- pressure difference measurement with the use of an external sensor
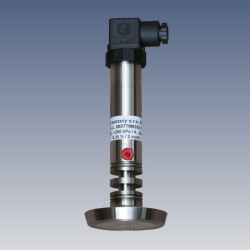
- for water,air, hydraulic systems, petroleum products, chemicals, etc.
- also with diaphragm chemical seal
- hydrostatic level measurement
- analog or digital output ignal
- sanitizable design (CIP)
- explosion-proof design (ATEX)
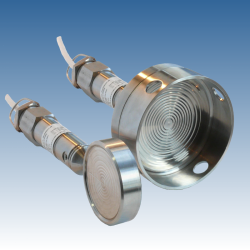
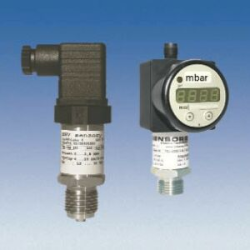
DMP 331, 333
DMK,LMP,LMK
- suitable for water and air applications, hydraulic systems, oil products, chemical compounds etc.
- material wetted parts: SS AISI316Ti, Viton, ceramics Al2O3